Enhance your daily operations with continuous
emissions and corrosion monitoring
mPACT2WO solutions enhance safety, compliance and operational efficiency
- reduce emissions
- minimize unexpected corrosion
- avoid over-monitoring and over-maintenance
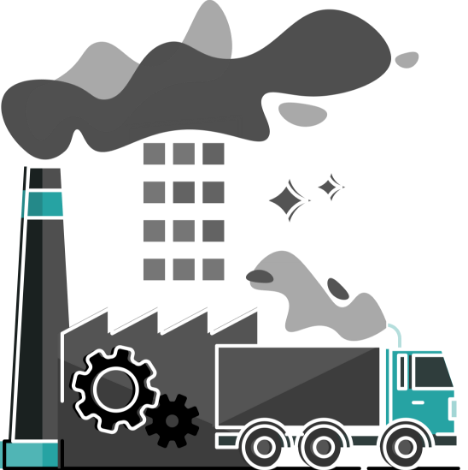
Refineries struggle to minimize or eliminate toxic emissions such as VOCs and air pollutants. Leaking components in refineries such as valves, pumps, compressors, and lines are a large source of VOCs and related emissions.
Refineries struggle with production wastage due to equipment leaks, impacts to safety and health, unplanned plant shutdowns with aging infrastructure and increases in maintenance costs.
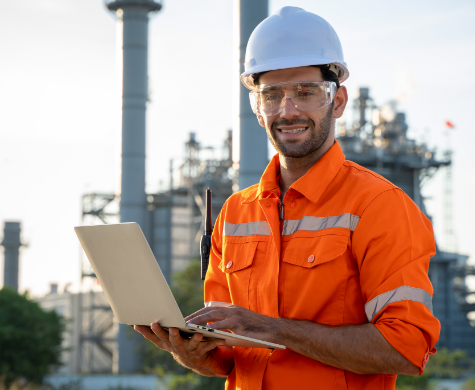
The oil and gas industry are faced with volatile organic compounds (VOCs) and fugitive emission challenges that vary significantly depending on asset mix (offshore versus onshore, gas versus oil, upstream versus downstream), geography, and local regulations and practices. Enhancing safety, compliance and operational efficiency are critical from unexpected corrosion, catastrophic events and unplanned maintenance.
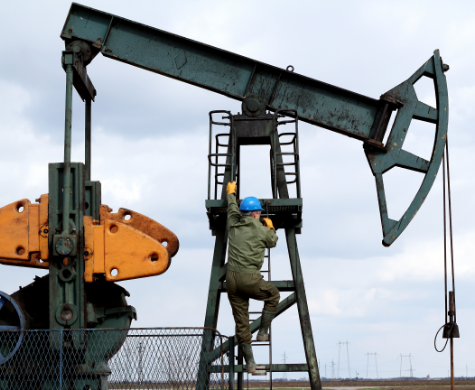
The petrochemical industry is experiencing high growth with increasing demand in automotive, consumer goods, medical, packaging, construction, and other industries. The industry is faced with minimizing and eliminating volatile organic compounds (VOCs) and fugitive emissions from feedstocks used in production of plastics, ammonia, synthetic rubber, glycol and others. In addition, the industry is faced with enhancing safety, compliance and operational efficiency from unexpected corrosion, catastrophic events and unplanned maintenance.
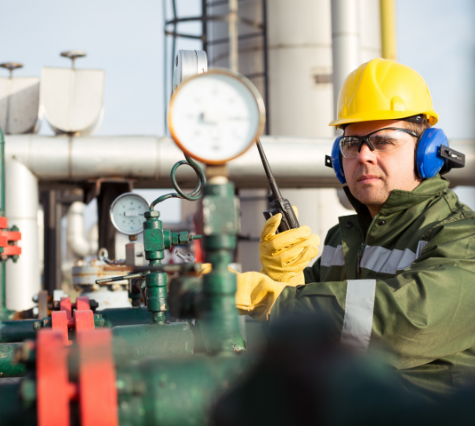
Operators can leverage data to enhance daily decisions with mPACT2WO solutions
EMISSIONS
Abnormal emissions impacting safety of the work environment.
mRegzTM AirCompliance for continuous emissions monitoring to enhance process safety.
Early indication and location information enabled operations to avoid potential unsafe condition.
This avoided potential unsafe condition and/or personnel exposure due to the abnormal equipment condition.
Corrosion
Process piping experiencing high corrosion rates.
mCluezTM Corrosion Monitoring to avoid unexpected corrosion and unplanned maintenance.
Combining high-accuracy thickness measurements with plant operations data helped to identify changes in corrosion rates early.
Real-time corrosion monitoring was able to show immediate improvement in corrosion loss once the corrosion inhibitor pump was returned to service.